Technology Insights
7 Signs You Need Better Hardware Management—And What You Can Do About It
By Denise Sarazin / July 14, 2025
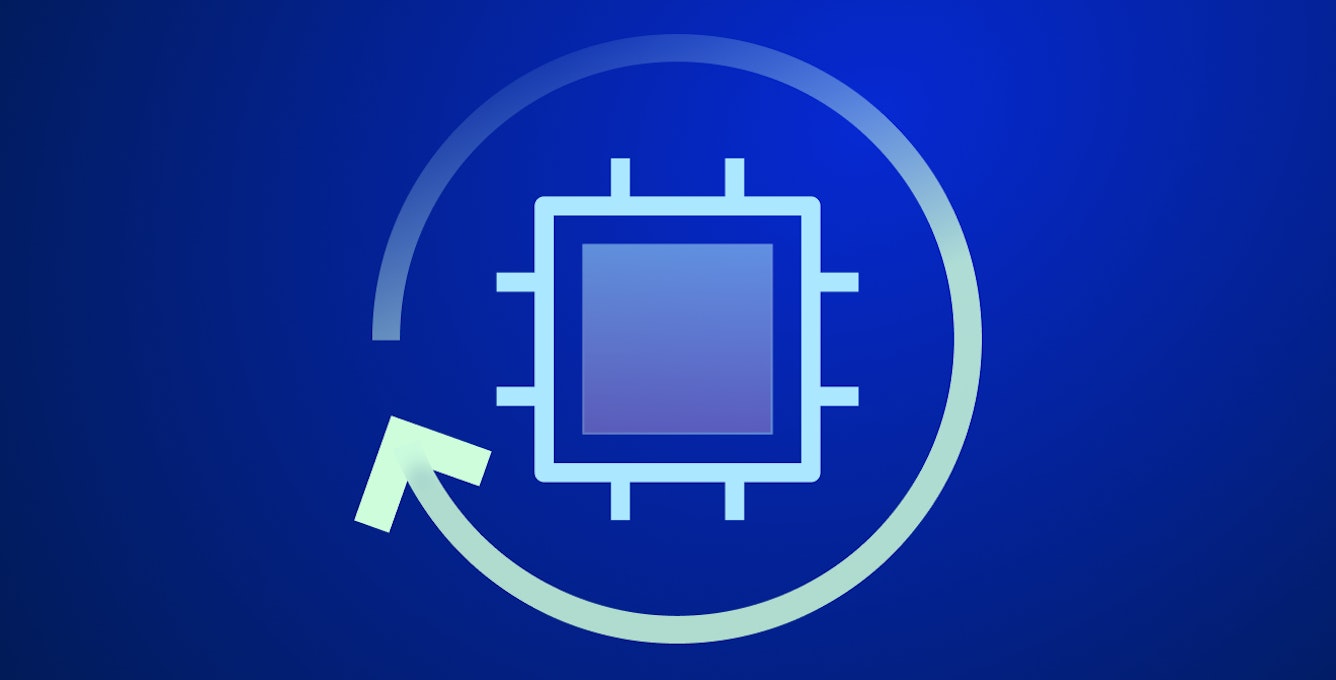
In this article:
Many businesses are struggling with hardware management without even realizing it. Recognizing the warning signs early can save time, costs, and frustration while improving security and employee satisfaction.
Managing hardware assets has become more complex than ever. The rise of remote and hybrid work models means devices are no longer confined within office walls, making it harder for businesses to maintain oversight and control. What used to be a straightforward task—distributing laptops and phones—is now a multifaceted challenge involving procurement, deployment, tracking, servicing, and secure retrieval across diverse locations.
While many organizations recognize the importance of hardware management, few realize how deeply inefficient and fragmented current systems can be—until problems start surfacing in the form of lost devices, budget creep, security risks, or frustrated employees. Without a clear strategy and the right tools, companies can quickly find themselves overwhelmed, risking security breaches and operational slowdowns.
This blog is designed to help decision-makers and IT professionals alike identify the warning signs that their hardware management needs a serious upgrade. We’ll unpack the root causes behind these challenges, explore why a single, integrated platform is rapidly becoming the game-changer in this space, and highlight the strategic benefits that go beyond just saving money. Whether you’re advising clients, managing IT operations, or simply looking to improve your company’s hardware workflows, this practical guide will provide actionable insights to help you take control of your hardware lifecycle from procurement to retirement.
About this article
This article is part of our Thrive Blog Series, offering a glimpse into the kinds of trends and insights we’ll be exploring at Thrive 2025 in Austin, August 25-27. Watch for new posts on our blog through August.
Spotting the warning signs: When your hardware needs an upgrade
1. Lost or misplaced devices
Keeping track of devices is a widespread challenge in IT asset management and not having full visibility is more than an inconvenience—it’s a significant financial and security risk. Gartner reports that about 30% of hardware assets are lost or unaccounted for in organizations, translating into millions in lost equipment and potential data breaches. This often happens without a clear process for tracking devices, especially as more employees work remotely or across multiple locations.
Root cause
A lack of centralized tracking systems and reliance on manual processes make it difficult to maintain updated records of device ownership and location. Dispersed workforces increase the risk of devices being lost, stolen, or forgotten.
Why you need to address this
Untracked devices lead to direct financial losses and potential exposure to data breaches, which can result in costly compliance fines and reputational damage. Additionally, replacing lost equipment drives up IT budgets unnecessarily.
30% of hardware assets are lost or unaccounted for in organizations, translating into millions in lost equipment and potential data breaches.
—Gartner
2. IT teams are overwhelmed with manual processes
Your IT staff might be spending excessive time juggling spreadsheets, manually updating asset registries, coordinating shipments, and chasing down missing equipment. This high-touch management drains valuable resources and limits IT’s ability to focus on innovation or strategic projects. Organizations without automation often face delays and errors that frustrate both staff and end users.
Root cause
Manual, fragmented workflows require IT teams to perform repetitive, time-consuming tasks across multiple tools and systems, increasing the likelihood of errors and inefficiencies.
Why you need to address this
When IT teams are bogged down with manual hardware management, they have less capacity for strategic initiatives, innovation, and timely support, which can slow overall business performance and damage employee satisfaction.
3. Poor visibility into asset location and lifecycle status
Without a centralized system providing real-time insights, it’s difficult to know where every device is, its condition, or when it needs maintenance or replacement. This lack of transparency leads to reactive decision-making, unexpected downtime, and inflated costs when old or unused devices are overlooked.
Root cause
Disparate systems or spreadsheets fail to offer a unified view of hardware inventory, resulting in data silos and outdated information about assets.
Why you need to address this
Lack of visibility increases the risk of service interruptions, security vulnerabilities, and unnecessary spending on replacement or maintenance, all of which can disrupt business continuity and productivity.
4. Frustrating, inefficient employee onboarding and off-boarding
Delays in equipping new hires or retrieving devices from departing employees hurt productivity and increase security risk. Manual shipping and retrieval processes often mean new staff wait days or weeks to get necessary tools—frustrating them from day one—while unreturned devices can linger in limbo, increasing asset loss.
Root cause
Inefficient coordination and absence of automation in hardware provisioning and retrieval create bottlenecks and inconsistent employee experiences.
Why you need to address this
Poor hardware workflows directly impact employee productivity, morale, and retention. Onboarding delays cause dissatisfaction. And unreturned equipment leads to financial losses and security gaps. One study revealed that a third of employees are likely to look for a new job if they’re forced to use outdated technology, and 80 percent of new hires who receive poor onboarding plan to quit.
5. Lack of integration with core business systems
When hardware management tools operate in silos, disconnected from HR or IT service management platforms, important workflow automation is lost. This fragmentation results in missed equipment assignments, delayed updates, and an increased burden on IT and HR teams to manually coordinate device provisioning.
Root cause
Legacy or fragmented systems without integration capabilities force manual cross-team coordination and duplicate data entry.
Why you need to address this
Disconnected systems increase operational complexity, create errors, and lengthen response times, impacting efficiency and employee satisfaction.
6. Rising IT costs due to redundant purchases and poor utilization
Inaccurate tracking leads companies to buy new devices unnecessarily because existing equipment is “lost” or underutilized. Without effective redeployment strategies or disposal planning, hardware budgets balloon as excess inventory accumulates or equipment reaches end-of-life prematurely.
Root cause
Inadequate asset utilization visibility and lack of lifecycle optimization cause overspending and waste.
Why you need to address this
Uncontrolled IT spending drains budgets that could be better invested elsewhere, while poor utilization leads to inefficiencies and environmental waste. To put it in perspective, fixing IT issues results in an average $3,165 of wasted productivity per employee per year.
7. Difficulty scaling support for remote, hybrid, or global teams
As companies grow geographically and embrace flexible work models, managing hardware becomes more chaotic and complex. The lack of a global, unified management platform means IT teams struggle to provision, track, and maintain devices seamlessly across locations—resulting in inconsistent employee experiences and operational inefficiencies.
Root cause
The absence of centralized, scalable systems limits the ability to provide consistent and efficient hardware support worldwide.
Why you need to address this
Failing to scale support adequately can cause business disruptions, slow growth, frustrate employees, and damage your company’s reputation as a modern workplace.
Key takeaway
Recognizing these signs is the first step toward overcoming the complex challenges of hardware management. Each issue, from asset loss to scaling difficulties, stems from fragmented systems and manual processes that no longer meet the demands of modern, distributed workforces. Addressing these pain points is critical not only to control costs and reduce risks but also to enhance employee productivity and satisfaction.
In the following section, we’ll explore how adopting a centralized hardware lifecycle management platform can provide an effective, scalable solution to these pervasive problems.
How a central platform can transform your hardware management
A centralized hardware lifecycle management platform automates and centralizes all stages of hardware asset management—from procurement and deployment to real-time tracking, maintenance, and secure retrieval. This level of hardware lifecycle automation eliminates manual inefficiencies and improves IT asset management.
Automation reduces manual work and frees up IT resources
A comprehensive platform automates the entire hardware lifecycle, freeing IT teams from time-consuming manual tasks such as updating spreadsheets, coordinating shipments, imaging devices, and tracking assets manually.
This automation enables zero-touch provisioning, ensuring devices arrive pre-configured and ready for use, allowing employees to simply open their device and log in.
Similarly, offboarding and retrieval processes are automated to ensure timely collection and secure data wiping, minimizing the operational overhead on IT teams.
By integrating seamlessly with existing business systems like HR and IT service management platforms, the solution automatically aligns device provisioning with employee onboarding and offboarding, eliminating manual ticketing and cross-team coordination.
This integration dramatically improves workflow efficiency and allows IT to operate at a vastly improved support ratio, sometimes supporting thousands of employees per IT staff member.
Real-time tracking improves visibility and asset control
Centralized dashboards provide comprehensive, real-time insights into the location, condition, and lifecycle status of every asset—whether on-site, in transit, or with remote employees worldwide.
This continuous tracking enables proactive maintenance, timely upgrades, and rapid detection of lost or misplaced devices.
The platform maintains a full, auditable history of each device, improving security and ensuring compliance during IT audits.
Additionally, automated tracking of global shipping, customs clearance, and delivery status ensures devices arrive and are retrieved efficiently anywhere in the world, removing logistical headaches and delays.
Seamless integration streamlines workflows and boosts collaboration
By plugging into core enterprise systems, the platform streamlines onboarding workflows from hardware requests to delivery without manual intervention. HR data drives provisioning, while IT teams receive automated alerts about asset status, reducing administrative burden and errors.
This unified approach eliminates silos and improves employee experiences by ensuring they have the right tools from day one and that devices are collected securely upon departure.
It also enables IT staff to stop wasting time on inefficient processes and spend time on more strategic tasks.
Enhanced security ensures compliance and protects data
With a centralized platform managing the entire asset lifecycle, organizations significantly reduce the risk of data breaches.
Automated data wiping and encrypted setups during device handoff protect sensitive information.
The system also generates certificates of destruction when equipment is disposed of or recycled, providing peace of mind and mandated compliance documentation.
Scalable solutions support remote and global workforces
As companies grow and adopt hybrid, remote, or global work models, a unified platform scales effortlessly to support thousands of employees across multiple geographies. It handles complex logistics, customs, and diverse vendor management seamlessly, ensuring consistent IT asset experiences worldwide without adding operational complexity.
Optimized lifecycle management cuts costs and promotes sustainability
Optimized asset utilization and lifecycle management reduce redundant purchasing and minimize waste.
The platform helps businesses extend device lifespan through redeployment and efficient servicing, contributing to lower IT budgets.
End-of-life equipment is responsibly recycled or disposed of, supporting sustainability goals and a reduced environmental footprint.
Consolidated hardware spending under one platform also improves budget predictability and financial governance.
Key features to look for in a hardware management platform
Choosing the right hardware management platform is critical to optimizing IT asset management and overcoming the challenges of fragmented, manual asset workflows. To maximize efficiency, security, and cost savings, organizations should prioritize platforms that offer comprehensive functionality covering the entire hardware lifecycle.
Following is a checklist of essential features that enable businesses to streamline operations, enhance visibility, and support modern, distributed workforces effectively. Use the checklist when you're evaluating hardware lifecycle management platform options.
Centralized lifecycle management—The platform should manage the complete hardware lifecycle—procurement, deployment, tracking, maintenance, retrieval, and disposal—in a single system. This eliminates fragmented workflows and provides end-to-end visibility and control.
Seamless integrations with business systems—Look for integration with HR, IT service management, and procurement platforms to automate onboarding, offboarding, and asset tracking workflows, reducing manual ticketing and coordination.
Automation and zero-touch provisioning—Automated workflows, including zero-touch device provisioning and automated retrieval processes, reduce IT manual workload, speed up employee onboarding/offboarding, and minimize errors.
Real-time tracking and visibility—Dynamic asset tracking across locations with live updates on device location, status, and lifecycle stage helps prevent loss, optimize usage, and plan timely maintenance or upgrades.
High asset retrieval and secure data handling—Features to ensure high retrieval rates of hardware during offboarding, combined with secure data wiping and compliance-certified disposal processes, reduce security risks and regulatory exposure. For example, companies using Firstbase to manage device refreshes and retrievals see a 97% retrieval rate and major cost savings.
Flexible procurement and budgeting options—Support for buying, leasing, or managing existing hardware within set budgets offers financial flexibility and cost control, helping reduce redundant purchases and optimize spend.
Self-service portals for end users—Employee self-service capabilities for ordering equipment improve satisfaction and reduce support tickets, ensuring users have the right tools from their first day.
Global logistics and compliance support—Capabilities to handle international shipping, customs clearance, and local regulations enable efficient hardware delivery and retrieval across global workforces.
Sustainability and responsible disposal—The platform should promote environmentally responsible practices such as device redeployment, recycling, and certified e-waste disposal to minimize carbon footprint.
Comprehensive reporting and audit trails—Maintain detailed, auditable histories of hardware assets for security, compliance, and operational insights, enabling easy IT audits and risk management.
Next steps to transform your hardware management
Assess how your current challenges and processes line up with those we've identified in this blog
Identify gaps and issues you want to address
Engage with a vendor that can provide a centralized, automated hardware lifecycle management solution and meets the criteria we've outlined
Thrive 2025: Take a deeper dive into hardware management practices
Want to hear how leading technology companies are solving their end-user hardware challenges? Join us at Thrive for our hardware management session, Solve costly hardware management practices from a single platform.
The session will be sponsored by Firstbase, whose founder Chris Herd will provide keen insights and food for thought to get you started on your hardware management journey.
Discover more trends and best practices at Thrive 2025, August 25-27 in Austin. Register today and check out the many other available sessions and panels.

Related Articles
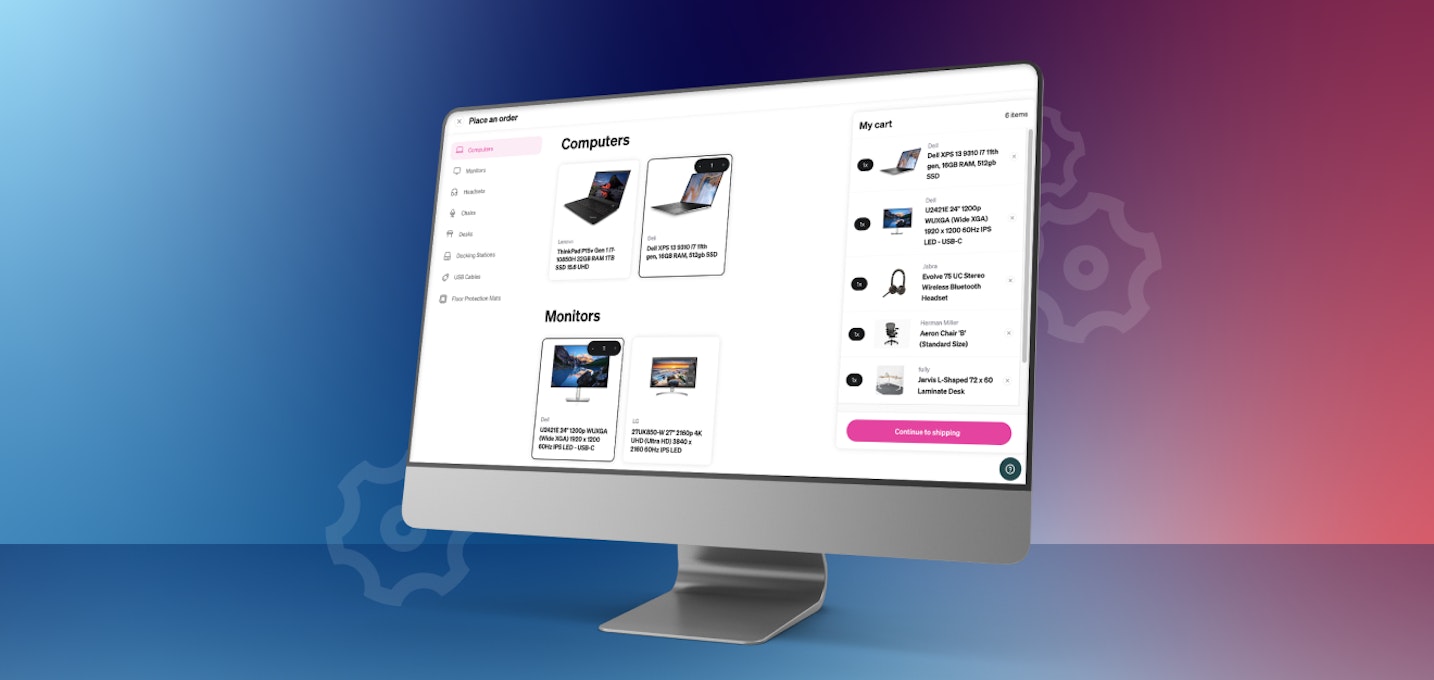
Strategy & Best Practices
Conquer Inefficient and Costly Hardware Management
Company hardware is often poorly tracked and plagued by manual processes, leading to 30% of hardware assets being lost, missing, or unaccounted for. Firstbase solves these problems with a platform that automates device management from procurement and onboarding, to offboarding and retrieval.By Denise Sarazin / AppDirect / April 7, 2025
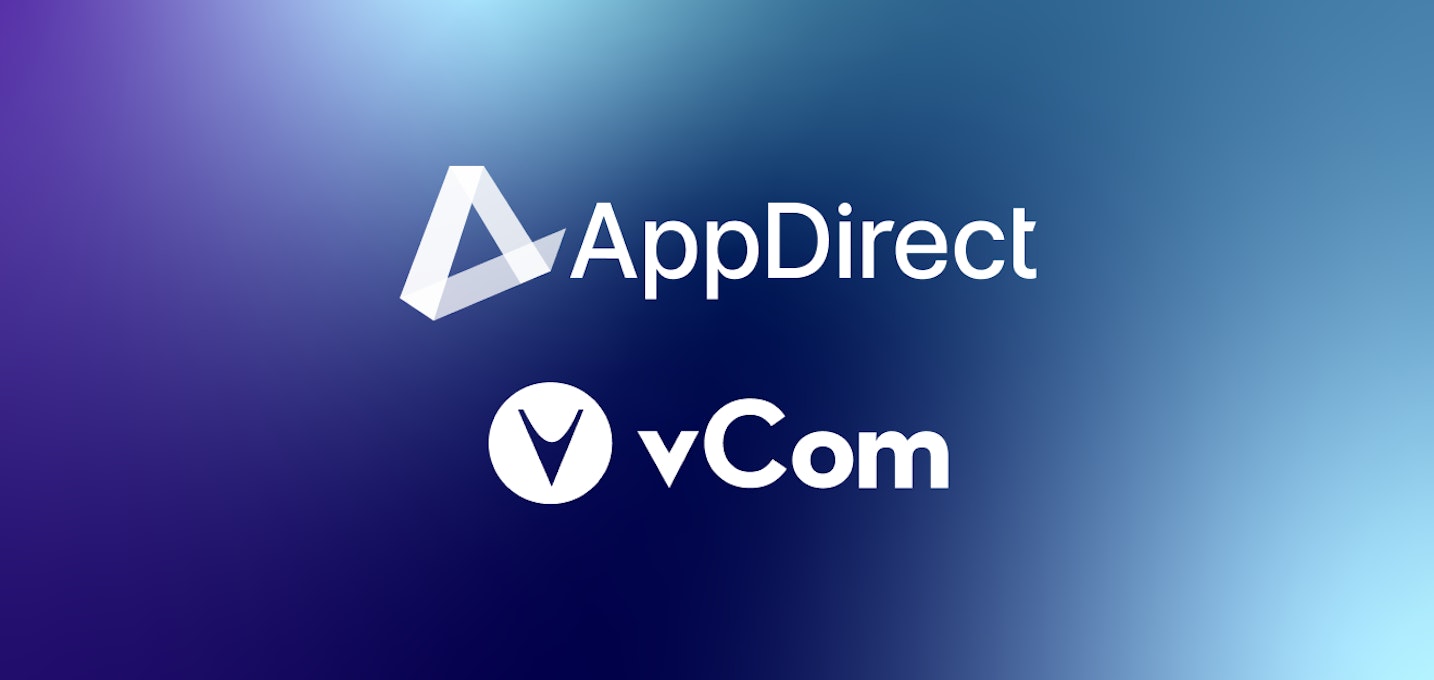
Strategy & Best Practices
How to Reduce Network and Mobility Costs by 30% with the Right Spend Management Tools
Up to 30% of IT budget dollars are wasted on unused or redundant technology due to poor tracking of IT expenses? Learn how network and mobility lifecycle management on a single streamlined platform helps businesses manage everything from planning and procurement to operations and expense management.By Denise Sarazin / AppDirect / March 3, 2025
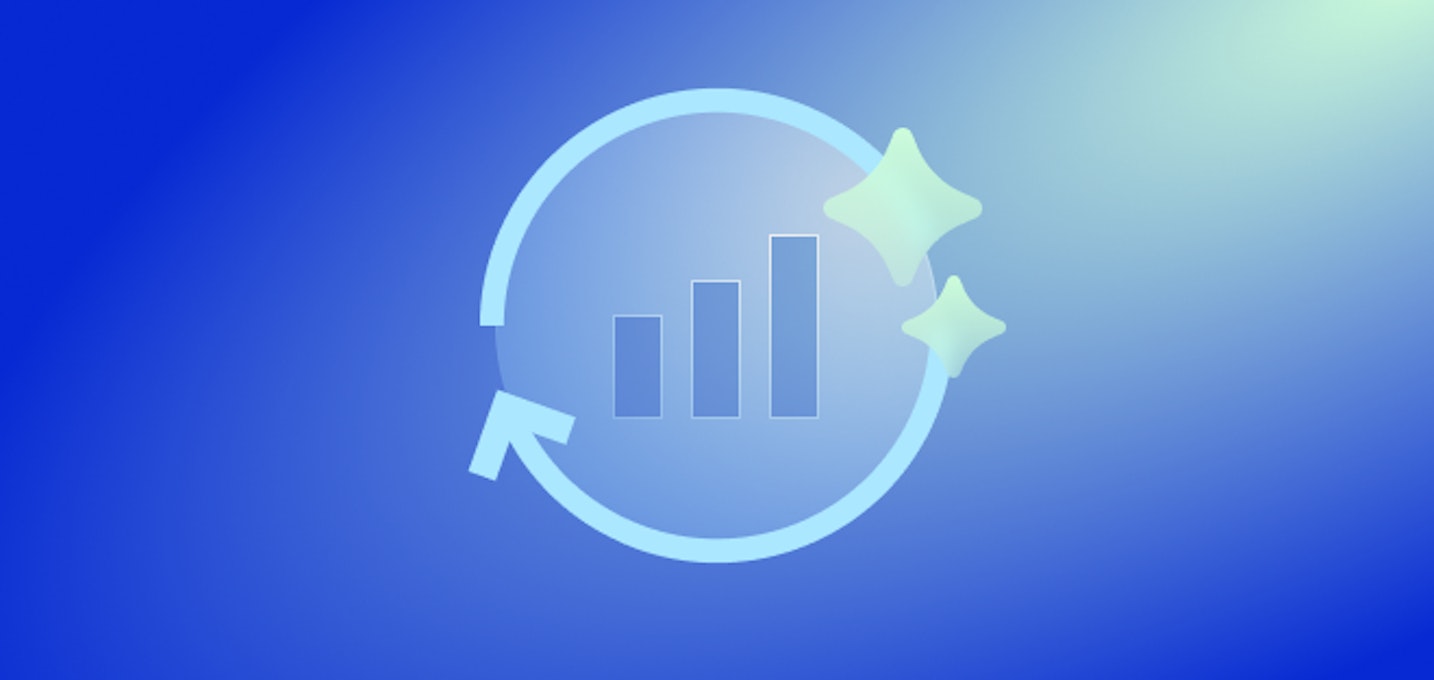
Strategy & Best Practices
Fast-Tracking AI Value: Strategies for Immediate Impact
Turn AI's potential into a profit-generating reality for your business. Discover how to pinpoint impactful AI opportunities, choose the right partners, and start generating immediate value.By Denise Sarazin / AppDirect / June 16, 2025